Wybór odpowiedniego grota do młota hydraulicznego marki DHB decyduje o efektywności prac w kamieniołomach, przy rozbiórkach obiektów przemysłowych oraz podczas modernizacji infrastruktury drogowej. Każdy typ grota ma swoje unikalne zastosowanie. W artykule zaprezentujemy różne rodzaje grotów i przyjrzyjmy się i ich specyficznym funkcjom.
Jak dobrać idealny grot do projektu?
Przy wyborze rodzaju grota należy wziąć pod uwagę kilka czynników:
- Rodzaj materiału do kruszenia
- Konkretne potrzeby danego zadania
- Kompatybilność z posiadanym młotem hydraulicznym
Podstawowe rodzaje grotów do młotów hydraulicznych
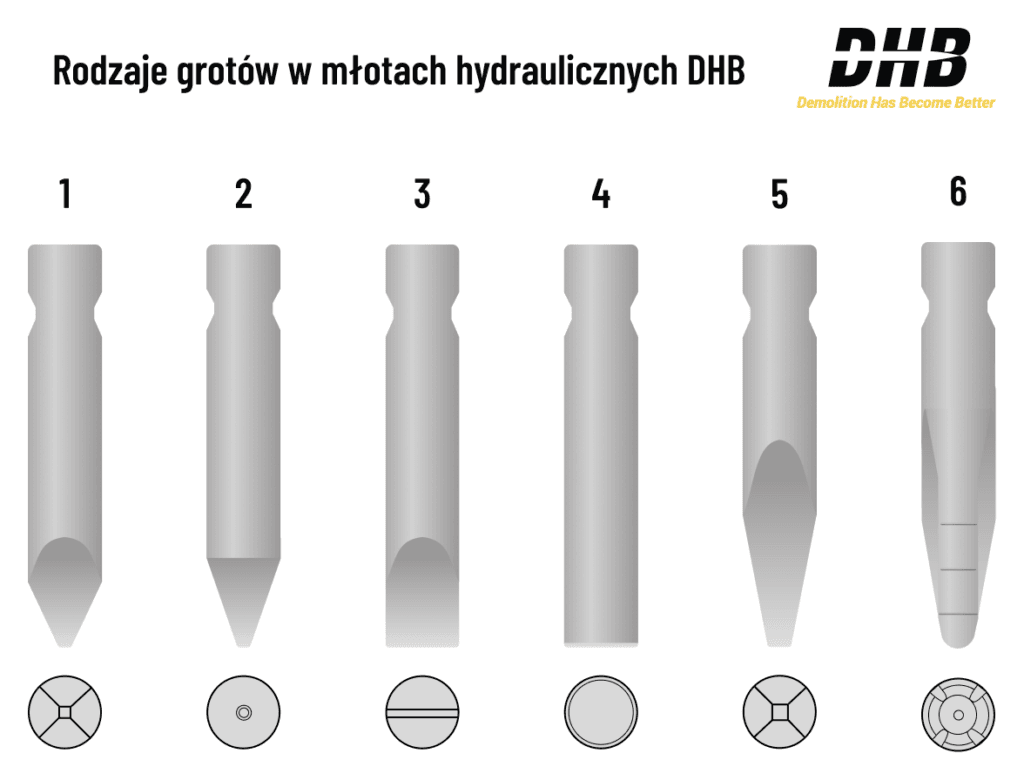
- Szpicak standardowy (Moil Point) to uniwersalny grot wielozadaniowy, idealny do kruszenia betonu i skał. Jego stożkowy kształt zapewnia doskonałą penetrację materiału.
- Grot stożkowy (Conical Point) to kolejny typ grota wielozadaniowego. Sprawdza się szczególnie przy pracach wymagających precyzji i dobrej kontroli podczas kruszenia betonu.
- Grot płaski (H-Wedge) to specjalistyczny grot przeznaczony do prac przy asfalcie, betonie oraz kopaniu rowów. Jego klinowy kształt generuje efekt rozłupujący i ułatwia precyzyjne cięcie materiału.
Groty specjalistyczne
- Grot tępy (Blunt) to grot tępy, stworzony do pracy z głazami. Zapewnia maksymalną siłę uderzenia przy kruszeniu twardych materiałów.
- Grot stożkowy (Conical Slotted) został zaprojektowany specjalnie do pracy ze skałami i betonem. Jego rowkowana konstrukcja zwiększa efektywność kruszenia.
- Szpicak kuty (Forged Moil Point) to wzmocniona wersja grota stożkowego, przeznaczona do intensywnej pracy przy skałach i betonie.
Kiedy wymienić grot w młocie hydraulicznym
Wymiana grota w młocie hydraulicznym to kluczowa czynność serwisowa, która ma bezpośredni wpływ na wydajność i bezpieczeństwo pracy maszyny. Pierwszymi sygnałami wskazującymi na konieczność wymiany są widoczne deformacje końcówki roboczej, nadmierne wytarcie powierzchni, a także pojawienie się zadziorów czy pęknięć. Szczególną uwagę należy zwrócić na stan trzonu grota, sprawdzając jego średnicę oraz miejsce, w którym uderza pobijak.
Narzędzie należy wymienić po zużyciu, gdy jego wymiary osiągną długość minimalną. Wartości dla tej długości dla młotów DHB prezentujemy w tabeli.
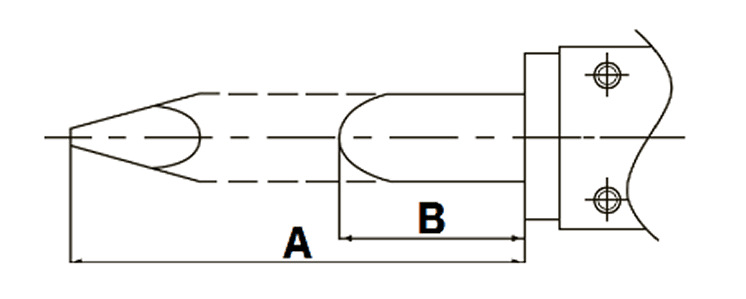
B to długość zewnętrzna, gdy narzędzie jest całkowicie wsunięte do korpusu.
Model | Oryginalna długość (A) | Długość minimalna (B) |
DHB 10S | 326 | 200 |
DHB 15S | 330 | 200 |
DHB 45S | 427 | 250 |
DHB 80S | 564 | 250 |
DHB 100S | 561 | 250 |
DHB 135S | 650 | 300 |
DHB 160S | 672 | 300 |
DHB 210S | 762 | 400 |
DHB 260S | 913 | 500 |
DHB 300S | 852 | 450 |
DHB 400S | 980 | 550 |
DHB 550S | 1020 | 600 |
DHB 650S | 1066 | 600 |
Zbyt późna wymiana grota może prowadzić do poważnych konsekwencji, takich jak zakleszczenie narzędzia w tulei prowadzącej czy uszkodzenie korpusu młota hydraulicznego. Rozhartowanie końcówki spowodowane przegrzaniem podczas intensywnej pracy, a także nadmierny luz między grotem a tuleją prowadzącą (przekraczający kilka milimetrów) to jednoznaczne sygnały do natychmiastowej wymiany narzędzia. Warto pamiętać, że koszt wymiany grota jest niewspółmiernie niższy niż potencjalne koszty naprawy uszkodzonego młota.
Zwiększ efektywność swoich prac wyburzeniowych
Dobór odpowiedniego grota znacząco wpływa na wydajność prac rozbiórkowych i wykopaliskowych. Niezależnie czy potrzebujesz grota uniwersalnego, płaskiego do precyzyjnego cięcia czy tępego do ciężkich prac wyburzeniowych – właściwe narzędzie zapewni optymalną wydajność.
Rodzaje grotów – podsumowanie
Młoty hydrauliczne w połączeniu z odpowiednim grotem to potężne i wszechstronne rozwiązanie dla szerokiej gamy zadań budowlanych i rozbiórkowych. Wybierz grot idealny do Twoich potrzeb, aby osiągnąć najwyższą precyzję i moc w realizowanych projektach.
Najczęściej zadawane pytania
Najbardziej uniwersalnym grotem jest grot standardowy (szpicak). Sprawdza się w wielu zastosowaniach, takich jak kruszenie betonu, rozbijanie skał czy prace drogowe, co czyni go wszechstronnym wyborem dla różnorodnych projektów.
Do kruszenia betonu najlepiej sprawdzi się grot standardowy (szpic) lub grot stożkowy przy grubszych warstwach.
W kamieniołomach, przy wydobyciu kruszyw, najlepiej sprawdzi się grot tępy, który maksymalizuje siłę uderzenia młota hydraulicznego.
Do prac w miękkich, nieściernych materiałach najlepiej sprawdzi się grot stożkowy, który minimalizuje zużycie narzędzia.